Traditionally, two-fold yarns have been used for weaving because they are stronger, and the twisting operation binds the surface fibers into the yarn structure so that it is smoother and more resistant to abrasion during weaving. The SiroSPUN™ process adapted some of the self-twist discoveries of CSIRO to the ring spinning technology of the worsted system, and combined spinning and doubling in the one operation. The technology maintains two separate strands during the spinning process, and this allows a number of fibre-binding mechanisms to operate before the strands are twisted about each other. An important aspect of the SiroSPUN™ system is a simple device to break out the remaining strand if one of the strands should be accidentally broken.
SiroSPUN™ is especially suited to the production of lightweight trans-seasonal fabrics, and a significant proportion of the world’s worsted spinning installations have been converted to this cost-saving and innovative CSIRO technology.
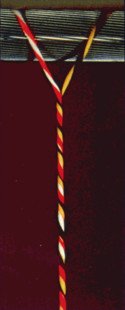
SIRO SPUN™ - SPINNING PROCESS
HOW WORKS SIRO SPUN™?
Spinners have long demanded spinning and twisting in a single operation. The SiroSPUN™ process offers the solution:
Two rovings are led separately through the drafting system in parallel and are only combined once they have passed the nip point of the front top and front bottom roller. A twofold-like weave able yarn, Siro yarn, is the result.
Two rovings are led separately through the drafting system in parallel and are only combined once they have passed the nip point of the front top and front bottom roller. A twofold-like weave able yarn, Siro yarn, is the result.
THE PROCESS
With the SiroSPUN™ process, a special spin-twisted yarn can be produced directly on the ring-spinning machine. In this process, two rovings are led in parallel through the drafting system, separated by two specially developed condensers, and drafted separately.
The twist is introduced as for a normal single yarn by means of ring and traveller. The roving strands, which are drafted parallel, are combined after passing the front rollers at the exit from the drafting system, with some twist being produced in the individual strands right up to the nip point. Once past the front roller of the drafting system, the two strands are combined producing a twofold-like yarn. The yarn has uni-directional twist like a singles yarn but the fibers are bound sufficiently for the yarn to survive weaving.
The twist is introduced as for a normal single yarn by means of ring and traveller. The roving strands, which are drafted parallel, are combined after passing the front rollers at the exit from the drafting system, with some twist being produced in the individual strands right up to the nip point. Once past the front roller of the drafting system, the two strands are combined producing a twofold-like yarn. The yarn has uni-directional twist like a singles yarn but the fibers are bound sufficiently for the yarn to survive weaving.
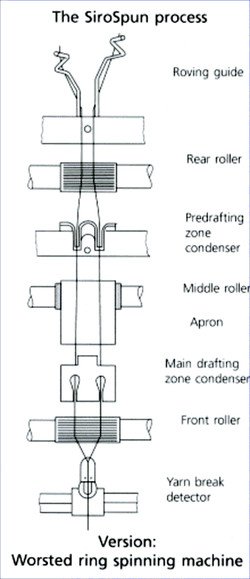
Controll
Half-weight single yarn sections are avoided by breaking the second strand if the other breaks. A mechanical yarn break detector located below the drafting system continuously controls the yarn path of both single yarns throughout the spinning process. If one of the two strands breaks, the special yarn break detector falls in the opposite direction, blocking the twist so that the second strand breaks, thus ensuring that only perfect Siro ply yarn runs onto the bobbins.
Spinning and twisting in a single direction
As well as it classical applications in long staple spinning, SiroSPUN™ has become established in the short staple spinning process.
far as the material is concerned, all the fibers with sufficient staple length normally used in long or short staple spinning can be processed. However, the twist used is similar to the normal two-fold twist rather than the normal singles twist.
Economic efficiency of SiroSPUN™
SiroSPUN™ is especially suited to the production of lightweight trans-seasonal fabrics, and a significant proportion of the world’s worsted spinning installations have been converted to this cost-saving and innovative CSIRO technology. ABARE estimated the benefits of SiroSPUN™ to the industry to be over $8 billion by 1992.
Half-weight single yarn sections are avoided by breaking the second strand if the other breaks. A mechanical yarn break detector located below the drafting system continuously controls the yarn path of both single yarns throughout the spinning process. If one of the two strands breaks, the special yarn break detector falls in the opposite direction, blocking the twist so that the second strand breaks, thus ensuring that only perfect Siro ply yarn runs onto the bobbins.
Spinning and twisting in a single direction
As well as it classical applications in long staple spinning, SiroSPUN™ has become established in the short staple spinning process.
far as the material is concerned, all the fibers with sufficient staple length normally used in long or short staple spinning can be processed. However, the twist used is similar to the normal two-fold twist rather than the normal singles twist.
Economic efficiency of SiroSPUN™
SiroSPUN™ is especially suited to the production of lightweight trans-seasonal fabrics, and a significant proportion of the world’s worsted spinning installations have been converted to this cost-saving and innovative CSIRO technology. ABARE estimated the benefits of SiroSPUN™ to the industry to be over $8 billion by 1992.
BENEFITS OF SIROSPUN™
SiroSPUN™ offers a number of benefits such as:
- reduces wool spinning costs by avoiding one stage
The main advantage of the SiroSPUN™ process is a reduction in spinning costs for pure fine wool weaving yarn. On average, SiroSPUN™ technology lowers the processing costs of spinning by 56 per cent. Weaving yarns are normally two-fold – that is, made up of two yarns twisted together. Ordinarily the strands must be first spun and then ‘two-folded’. SiroSPUN™ reduces cost by combining spinning and two-folding, allowing a twofold-like yarn to be produced in one step from wool top.
- advantageous to fabric producers
The economic effects of SiroSPUN™ are not restricted to the wool spinning stage. Fabric producers are also affected, in three principal ways. First, SiroSPUN™ yarns have slightly different weaving characteristics from conventional yarns, and this increases the costs of weaving by about 1 per cent. Second, because SiroSPUN™ yarns can be produced at a significantly lower cost than conventional yarns, part of this cost saving is passed on to fabric producers. The second effect outweighs the first, resulting in a net saving to fabric producers. Third, SiroSPUN™ fabrics have distinct quality characteristics.
- advantageous to garment makers, and wool growers
Cost savings at the fabric stage are passed down the processing chain to pure wool garment makers. The net effect is lower costs of producing wool garments and hence stimulation of consumer demand for wool products. This increase in final garment demand is, in turn, passed back up the production chain, increasing the demand for greasy wool, thus resulting in a higher price which benefits wool growers.